The working principle of the rotary blower is mainly based on the motor driving the impeller to rotate, thereby generating airflow. Its core components include the motor, impeller, inlet, outlet, etc. During operation, the motor rotates the impeller through the drive shaft, and air is sucked in from the inlet. After being compressed by the rotation of the impeller, it is discharged to the outlet, thus completing the ventilation and air exchange.
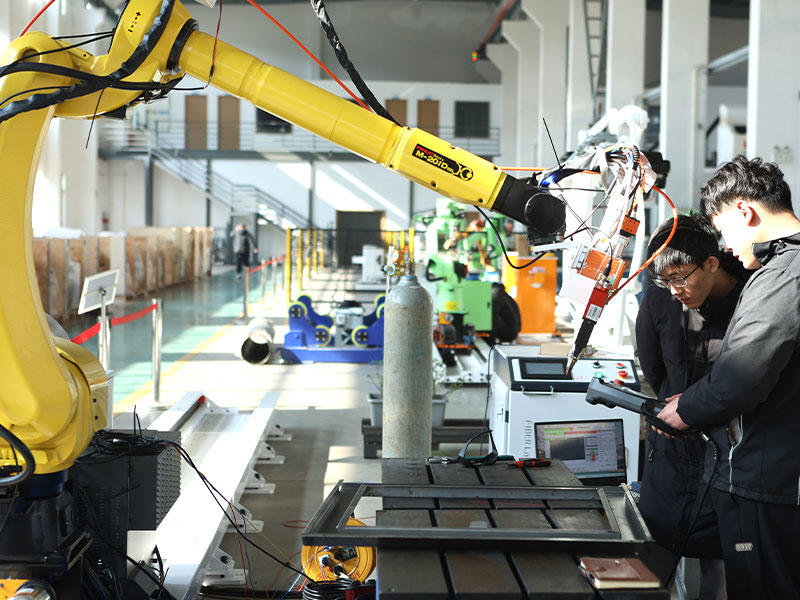
In terms of industrial adaptability, the rotary blower is widely used in various fields such as metallurgy, chemical industry, electric power, environmental protection, etc., due to its high efficiency, stability, and ease of maintenance. In the metallurgical industry, rotary blowers can be used for ventilation and air exchange in equipment such as blast furnaces and converters; in the chemical industry, they can be used for waste gas treatment, ventilation, and deodorization; in the electric power industry, they can be used for ventilation and heat dissipation of boilers, cooling towers, etc.; in the field of environmental protection, they can be used for exhaust gas treatment in processes such as sewage treatment and garbage incineration.
In the future, with the continuous development and innovation of industrial technology, rotary blowers are expected to be further optimized and improved in terms of performance, structure, materials, etc. For example, by adopting advanced control technology and intelligent systems, real-time monitoring and automatic adjustment of the blower's operating status can be achieved, further improving its operating efficiency and stability. At the same time, the use of new materials and manufacturing processes can reduce the energy consumption and noise of the blower, and improve its service life and reliability.