Precisely designing the geometry, number of blades, and cross-sectional shape of the impeller can optimize the gas flow path, reducing gas flow resistance in the impeller. Using computational fluid dynamics (CFD) methods for three-dimensional flow field analysis can simulate and evaluate the effects of different design parameters on gas flow, thereby determining the optimal impeller design.
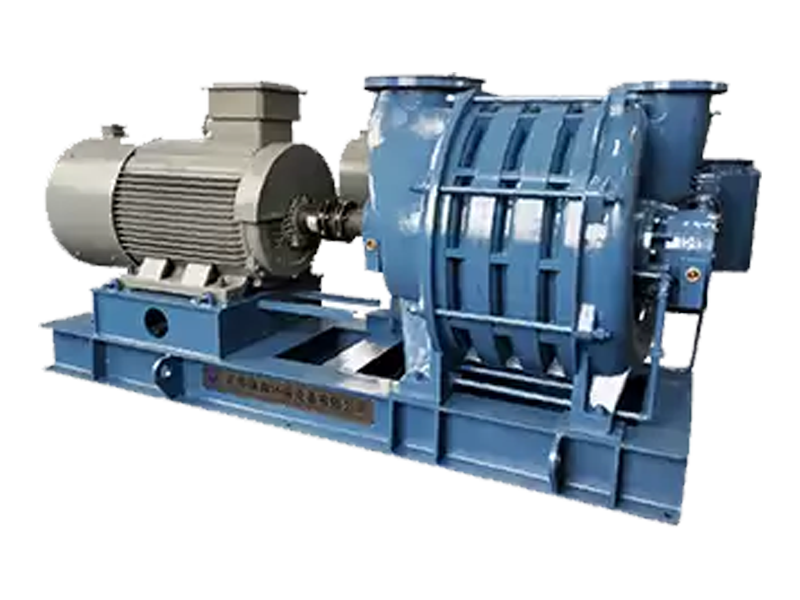
The match between the rotor and stator has a significant impact on the performance of the blower. Precise design and manufacturing to ensure a reasonable gap between the rotor and stator can reduce internal leakage and friction losses, thereby improving efficiency.
Optimizing the internal sealing structure of the blower to reduce gas leakage. Using high-quality materials and manufacturing processes to reduce friction and wear of mechanical components, thereby reducing energy losses.
Using intelligent control systems to adjust the operating parameters of the blower, such as speed and air intake, according to actual working requirements, to avoid unnecessary energy consumption. Through real-time monitoring and diagnostic functions, potential problems can be detected and addressed promptly to ensure that the blower operates at its best state.
Regular maintenance and servicing of the blower, including cleaning, inspection, and replacement of vulnerable parts, can ensure its long-term stable operation, reducing efficiency degradation caused by wear and aging.
Multistage centrifugal blowers can effectively reduce resistance loss and improve efficiency through methods such as optimizing impeller design, airflow guiding devices, improving match, reducing internal losses, adopting advanced control systems, and regular maintenance and servicing. The application of these methods not only improves the performance of the blower but also extends its service life and reduces operating costs.